HPA First Project is our Smart SX Technology in action, and at scale. Solvent extraction has long been a method for extracting and purifying metals, but it’s not been successfully applied to aluminium until now. With the HPA First Project, we’re applying our proprietary licensed solvent extraction and refining technology to produce >99.99% pure aluminium products from a common industrial feedstock.
world looks at alumina.
Alpha HPA is committed to commercialising new, smarter technology to meet the growing demand for high purity alumina (HPA) using the most environmentally responsible and efficient methods. Central to our business is the development of our new Gladstone based HPA First Project where we will produce a range of low carbon footprint high purity aluminium products for a myriad of applications whilst creating opportunities for local communities.
Alpha HPA is committed to commercialising new, smarter technology to meet the growing demand for high purity alumina (HPA) using the most environmentally responsible and efficient methods. Central to our business is the development of our new Gladstone based HPA First Project where we will produce a range of low carbon footprint high purity aluminium products for a myriad of applications whilst creating opportunities for local communities.
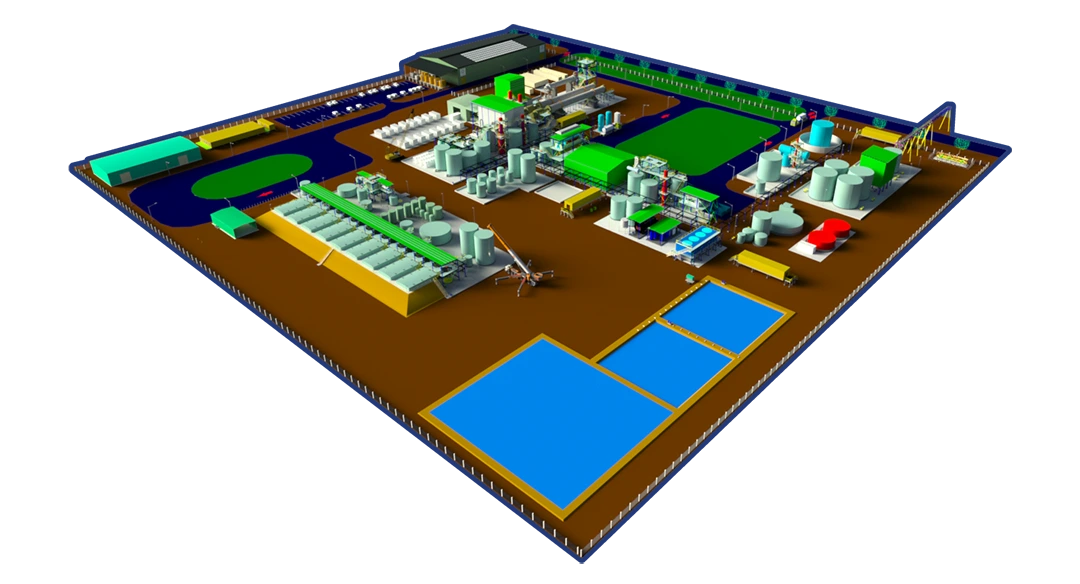
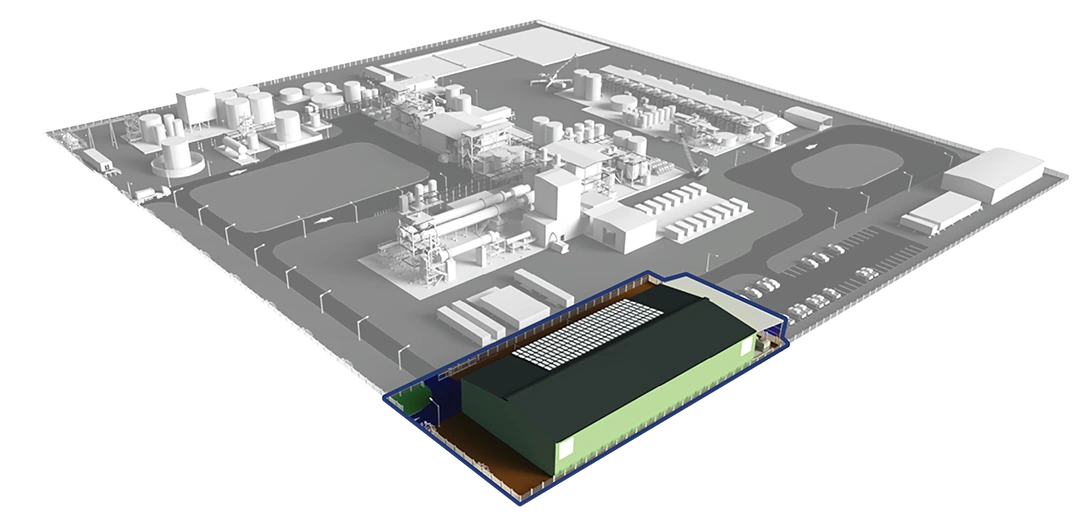
Market interest and numerous end-user discussions have enabled us to advance our HPA First Project revenue forward, through the construction of a Precursor Production Facility (PPF).
This facility will focus on the manufacture and sales of our 5N Ultra Aluminium Precursor salts, namely:
- Ultra Aluminium Nitrate (99.999% purity); used for various speciality applications including coatings, LED and laser phosphors, lithium ion battery electrode coatings and scintillators etc.
- Ultra Aluminium Sulfate (99.999% purity); used predominantly for the synthesis of aluminium-bearing lithium-ion battery cathode active materials (eg: NCA and NCMA).
Our facility will have a total Ultra Aluminium Precursor production capacity of ~ 10-20MT per month, with construction taking place on the same site as the HPA First Project in Gladstone.
For more information click here.
Our Gladstone facility will be a platform to demonstrate new, greener opportunities—through our product, our processes, and our self-sustainable main administration building. The 10-hectare, state-of-the-art facility will leverage the latest in process control systems and automation, and will be capable of producing 10,000 tonnes of HPA equivalent per year. As we make this happen, we expect to create 120 full time jobs in the operational phase and over 300 jobs during construction. In short, our HPA First facility will be one of the largest single HPA refineries in the world.
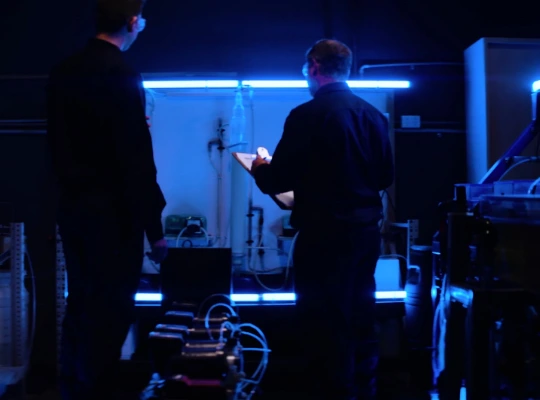
In July 2018, the technology behind HPA First Project was adopted as a major advance on the previous process flowsheet, which used a feedstock generated from the acid-leaching of laterite mineralisation from the Collerina Ni-Co-Sc Project, in central NSW.
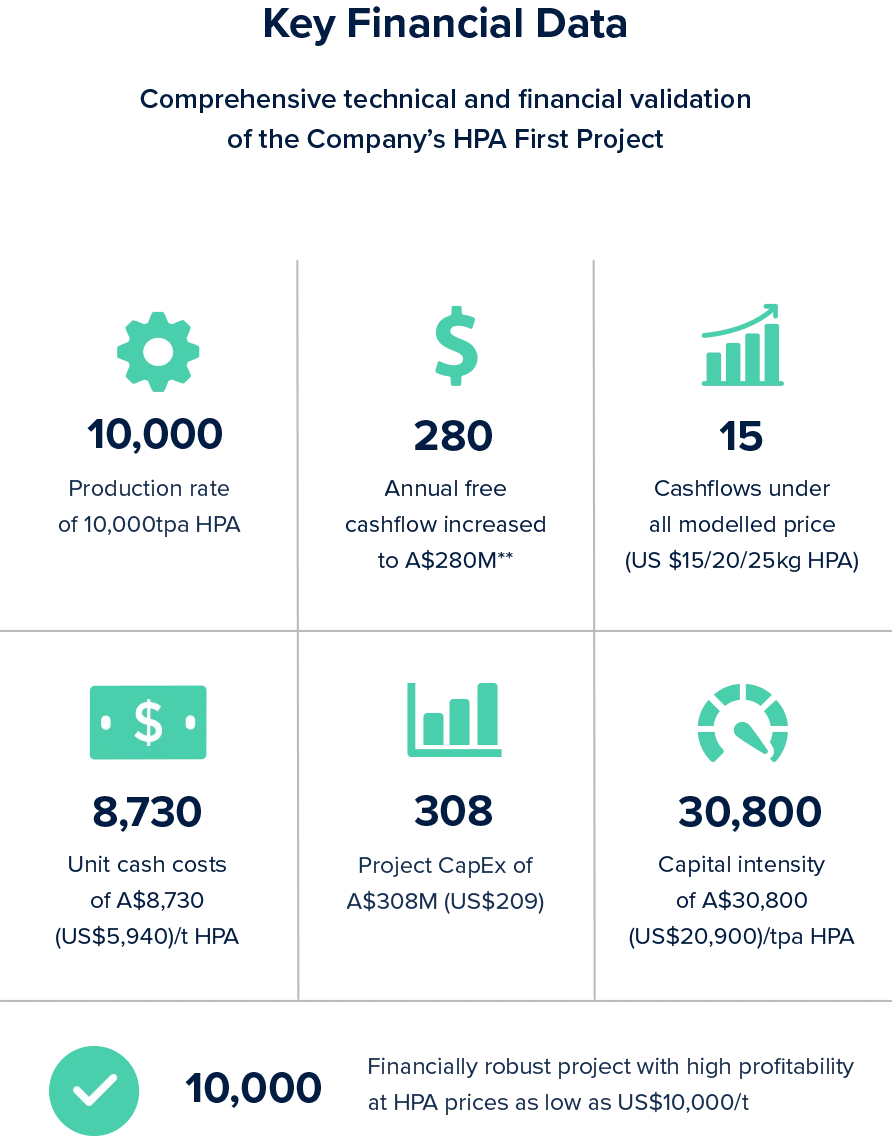
The HPA First Project Definitive Feasibility Study (DFS) was delivered in March 2020 and provides a technically robust and compelling business case:
Currently, around 83% of the world’s HPA supply comes from the Asia Pacific (APAC) region, with China the most prolific producer. Large, diversified chemical companies dominate this production, and generate HPA as a secondary product.
Our HPA First Project represents a large volume, single source, HPA production proposition, providing enormous opportunity. Alpha HPA has the potential to become the alternative supply source to the existing dominant producers. More importantly, Alpha HPA is well placed to fill the expected supply shortage as forecast HPA demand escalates over the next decade.
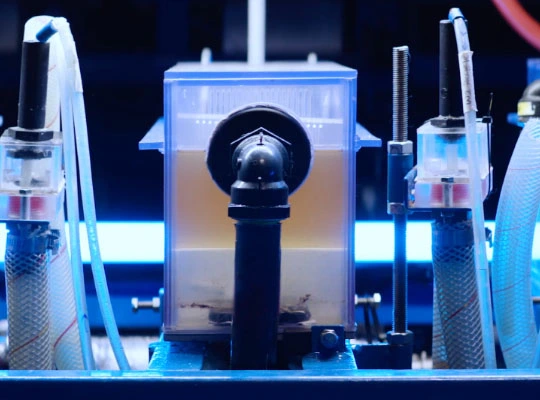
Alpha HPA has accumulated over 2000 hours of operations on its pilot and demonstration plant located in Brisbane. The demonstration plant has been upgraded to provide exceptional insight into the broader challenges with scaling up a process to the extent that Alpha HPA is confident that scale up risks are well understood and resolved.
By-products that come out of the extraction process can all be recycled so that almost makes us as a zero discharge facility.
What makes our Smart SX Technology the most sustainable, high purity alumina process technology in the world? Watch our short video to find out.
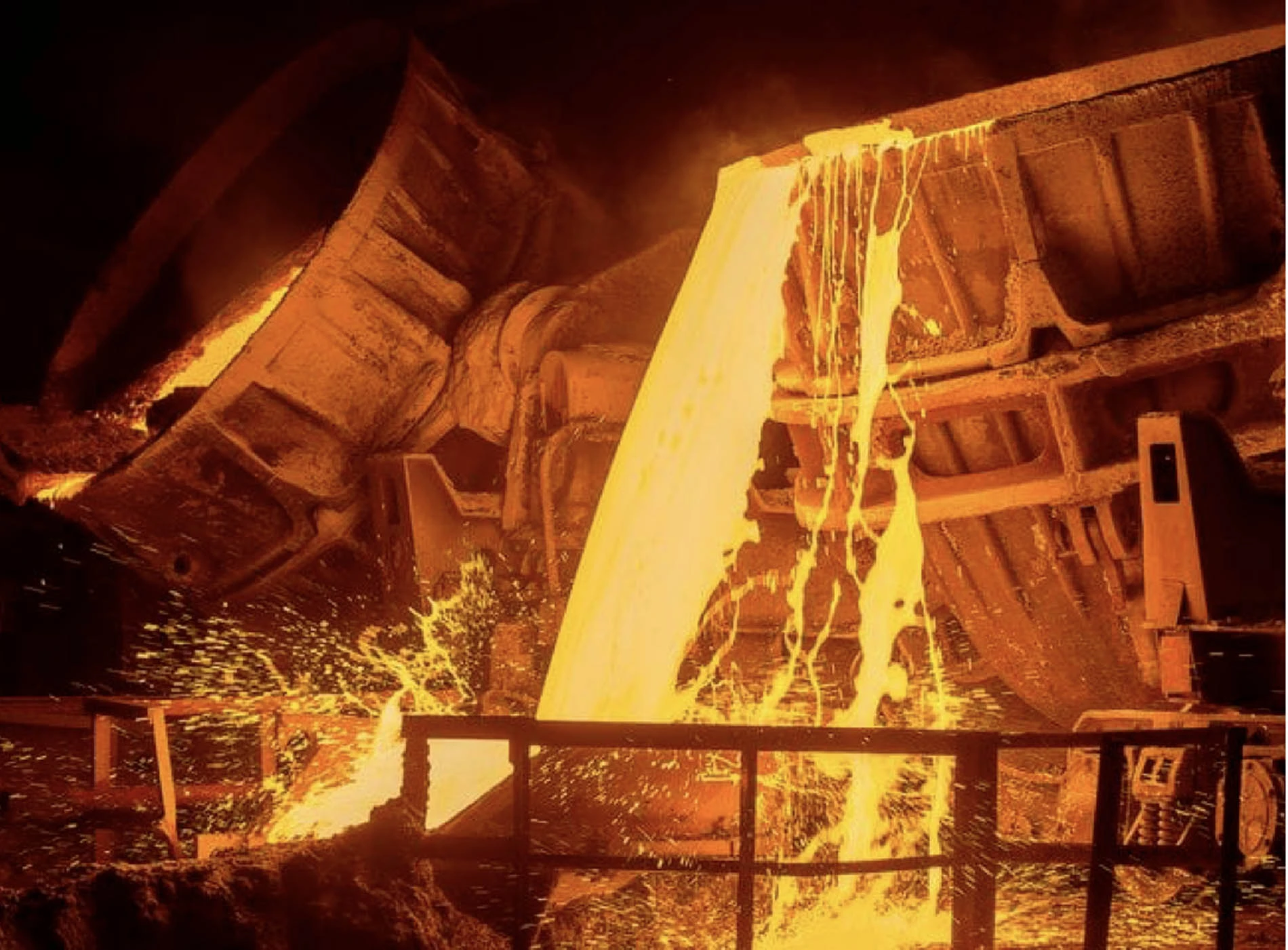
The standing methods for producing HPA lean on old technology. Under existing processes, HPA production is synthesised from aluminium metal feedstock, or produced from hydrochloric acid leach of kaolin clay. Both of these processes are energy intensive, produce high emissions, and create a significant amount of waste. Not only is this detrimental to the environment, it’s inefficient.
The unique Smart SX Technology is a highly selective scientific process that enables us to extract aluminium with pinpoint accuracy, and to generate a suite of Ultra High Purity aluminium products at a very low carbon footprint. This process gives us the flexibility to make products that others simply cannot match. Furthermore, 100% of its reagents are recycled into a saleable by-product, which puts us at an almost zero discharge facility.
Process Flowsheet
The HPA First Process Flow sheet is simple, ingenious and flexible, capable of purifying a common industrial feedstock into a range of ultrapure aluminium products at high efficiency and low cost.
The flow sheet uses no novel units of operation, but instead employs unique, proprietary process chemistry to deliver the first aluminium SX facility in the world.
- Nov '18 - Feb '19
-
Pre Feasibility Study
Complete
- July '19 - Mar '20
-
HPA First Pilot Plant – 600+hrs operation, > 40kg HPA Production
Complete
- Nov - Dec '19
-
Market Outreach – HPA samples despatched to the LIB supply chain
Complete
- Mar '20
-
Chemical Counterparty Agreement with Orica – Gladstone Project Location
Complete
- Mar '20
-
Definitive Feasibility Study – completed March 2020
Complete
- April '20
-
Commencement of Project Permitting and Financing
Complete
- June '20
-
First-stage testing approval by US-based Li-B separator manufacturer
Complete
Complete
- June '20
-
First test order received from Taiwan based sapphire glass manufacturer
Complete
Complete
- Aug '20
-
Offtake, marketing & financing MOU with Traxys
Complete
Complete
- Sept '20
-
High-purity (5N) Li-B Pre-Cursor manufacture confirmed
Complete
Complete
- Nov '20
-
Alpha HPA signs MoU with Rhineland
Complete
- April '21
-
Alpha HPA signs MoU with Saint Gobain Ceramics and Plastics
Complete
- Apirl '21
-
Alpha HPA signs MoU with APL Engineered Materials
Complete
- April '21
-
Alpha HPA signs MoU with Cleanco Queensland
Complete
- May '21
-
Alpha HPA signs MoU with Technologica
Complete
- June '21
-
Alpha HPA accelerates production with the fully-funded Precursor Production Facility
Complete
- Aug '21
-
Orica definitive chemical counterparty agreement executed for reagent supply and by-product offtake for the HPA First Project.
Complete
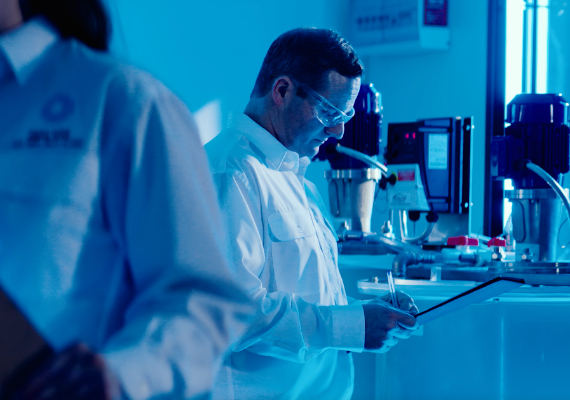
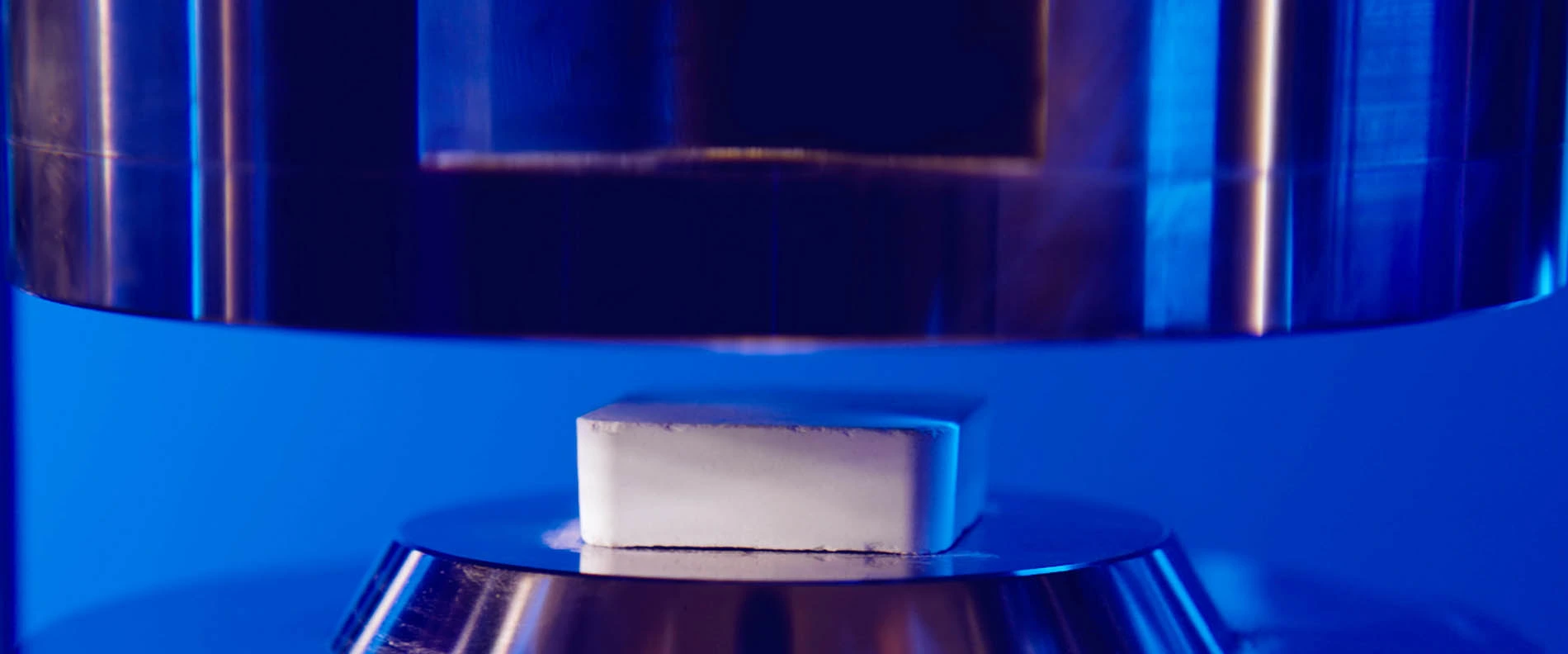
